Valve is an indispensable process component in the fields of modern petroleum, chemical industry, and natural gas. It plays the role of diversion, cut-off, throttling, check, and diversion. However, since most of the working media of the valve are toxic or highly corrosive substances, once leakage occurs, casualties may occur, so the safety of the valve is particularly important.
Most of the medium passing through the valve has high pressure, a large temperature range, and strong corrosiveness, so the quality of the valve is very high. Only by facing up to the problems and hidden dangers in the quality inspection of the valve production process, and formulating corresponding measures, can the emergence of hidden safety hazards be avoided.
What is Forged Steel Material?
Forged steel is a material resulting from alloying iron and carbon under extremely high pressure. Forged steel has less surface porosity, a finer grain structure, more tensile and fatigue strength, and greater ductility than any other processed steel.
Steel forgings are made out of alloying carbon and iron. Forged steel is produced under extremely high, yet accurate, pressure. It has better ductility than other manufactured steel, possesses fatigue strength, more tensile, has an advanced grain structure, and has less surface porosity.
What is Forged Steel Ball for Forged Steel Ball Valve?
Our forged steel grinding balls commonly used low-carbon alloy, high manganese steel, high carbon, and high manganese alloy steel. On the basis of this material, we have developed a series of competitive and efficient patent forged grinding balls.
Production Process of Forged Steel Ball
- Steel bars
- Production of the bar with the ideal chemical composition
- Billet
- Modern high-quality ovens
- Forging
- The forged ball with the highest mass found in the market
- Quenching
- The thermal treatment process provides hardness to the product
- Tempering
- This process eliminates the stress generated during the forging and quenching processes
- Final Product
- Packed in super sacks (no additional cost)
Materials used for Metal Seated Forged Steel Ball Valve
It should be able to meet the pressure of the on-site medium and the mechanical properties of the medium. The material needs to have the ability to resist the chemical and physical properties of the medium, and also needs to consider the economy of the valve.
In some media environments, lower-cost materials can be selected to avoid waste. In some high-temperature and high-pressure medium environments, it is necessary to select high-cost high-temperature resistant materials to meet the on-site use environment.
In field use, it needs to meet the requirements of reliable installation and flexible and reliable action. All this is inseparable from the control of the production process. Because the valve has many parts and a complex structure, different parts are completed by different processing techniques. Such as casting, forging, machining, heat treatment, welding, and other processes.
The inspection methods of parts manufactured by different processes are also different. For example, forged parts are mostly inspected by non-destructive testing, while the heat treatment is inspected by hardness testing.
Generally speaking, the valve manufacturing quality of forged steel valve manufacturers includes the blank quality of parts, processing size requirements, surface roughness, and installation accuracy requirements.
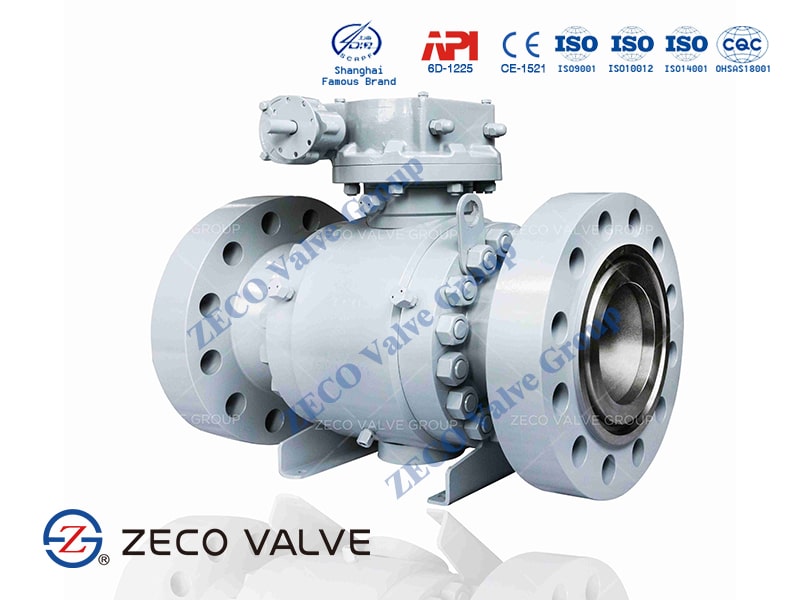
Pressure Test of Metal Seated Forged Steel Ball Valve
This is an essential test for every valve. When performing a pressure test on the valve, the inspector must check carefully, and the holding time and pressure must meet the requirements.
In order to improve the production speed, some forged steel valve manufacturers shorten the pressure holding time of the valve or fail to meet the standard requirements, resulting in inaccurate pressure test inspection of the valve. There are also some inspectors who do not understand the upper seal inspection test in place during pressure inspection and confuse the upper seal and packing structure.
In fact, the upper seal test is mainly to test the conical and spherical hard seal between the forged steel ball valve stem and the upper seal seat on the basis of the valve is fully opened.
Recommendations for pressure testing: When looking for leaks, the inspector cannot use the pressure curve as the criterion for the failure of the valve, but needs to analyze the valve, so as to accurately find the leak location and analyze the cause.
Statistical work should be carried out for leakage points, pay attention to grasp the location of easy leakage, and timely feedback to relevant units. For the operation of the inspectors, it must be safe and reliable. It is necessary to let the inspectors understand the principle of the pressure experiment so that the inspectors can interpret the pressure experiment more accurately.