On February 16, 2014, the B furnace of JSW DOLVI coking project of India contracted by SINOSTEEL EQUIPMENT successfully pushed coke in one time and produced qualified first-class coke. JSW DOLVI 1,000,000 ton coking project in India consists of two 5.5-meter ramming coke ovens and chemical production and recycling sections, which is the first production of 5.5-meter ramming coke ovens exported by a Chinese enterprise to India. In recent years, SINOSTEEL EQUIPMENT in the Indian market has built siscol400,000 tons of non-recycling coke ovens, jsw1.5 million tons of ramping coke ovens and supporting facilities, JSW 1.9 million tons of ramping coke oven and supporting facilities, USHA MARTIN 400,000 tons of non-recycling coke oven.
ZECO VALVE provided lug butterfly valves, cast steel gate valves, motorized ball valves, and some other industrial valves.
Who is JSW Dolvi?
The 10 MTPA integrated steel plant at Dolvi is advantageously located on the West coast of Maharashtra. It is connected to a jetty that can handle cargo of up to 15 MTPA.
JSW Dolvi Works is India’s first to adopt a combination of Conarc Technology for both steel-making and compact strip production, aiding the production of hot-rolled coils. From automotive and industrial to consumer durables, Dolvi manufactures products that meet the needs of companies across sectors.
JSW Dolvi Work
Located on the West coast of India, the plant has a jetty that can handle a capacity of 10 million tonnes per annum.
This provides the unit with logistical advantages in importing raw materials and exporting finished products. Located around 80 km from Mumbai, the unit is well connected via rail, road, and sea and has given JSW Steel a strategic presence in Western India.
The Dolvi Steel Plant caters to several industries including automotive, infrastructure, construction, machinery, LPG cylinder-manufacturers cold rollers, the oil and gas sectors, and consumer durables.
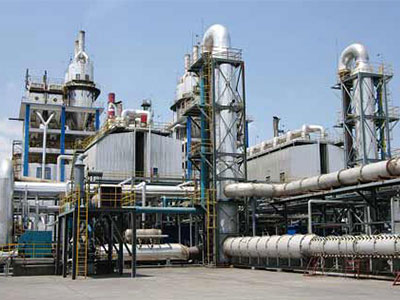
What is Coke Plant?
To make steel in a blast furnace, coal must first be turned into coke. Coke has a dual role in the steelmaking process. First, it provides the heat needed to melt the ore, and second, when it is burnt, it has the effect of ‘stealing’ the oxygen from the iron ore, leaving only the pure iron behind. In the coking plant, coal is heated in the absence of oxygen to 1250c. This removes any impurities in the coal, resulting in coke, which is a porous substance that is nearly all carbon.
How does a Coke Plant Works?
Coal is the main ingredient used to make coke. Iron is produced by inputting coal into a blast furnace. However, coal cannot be put directly into a blast furnace because of all the harmful by-products that come from that. So, there is an intermediate process that occurs. Coal is converted into coke first. Coke is used as fuel in a blast furnace. It plays an important role in the chemical processes that take place in a blast furnace.
Coal is heated to about 1250 degrees Celsius in the coke ovens. This process is referred to as ‘dry distillation’ because these coke ovens are oxygen-free, so the coal does not actually burn. This process takes around 18 hours to convert 35 tons of coal into 25 tons of coke.
After heating up the coal into coke, the coke is then unloaded from the oven by a pusher machine. The pusher machine has a pusher arm that puts the coke into a car that takes the coke to a coke quenching tower. Here, the coke is quenched with water. The coke is then taken to a coke wharf, where the remaining water evaporates. A reclaimer then feeds the coke from the wharf to a conveyor belt, which transfers the coke to the crushing and screening station. The finished product is about two-thirds the weight of the original raw material.
During the distillation process, a large amount of gas and smoke is generated, which, after purification, creates coke oven gas, and other by-products such as ammonia, tar, sulfur, naphthalene, and benzol. The creation of coke and the purification of gas are performed completely automated.
Coke makers use a mix of coal to improve the quality of coke they create. High-quality coal does not generate high pressure on the coke oven, and they also shrink enough so that they are easily removed from the coke oven. The properties of coke are influenced by moisture content and density.
The main use of coke is to make iron. The burning of coal to coke produces carbon monoxide. A touch at the bottom of the furnace allows impurities to flow out of the furnace. This, coupled with the fact that many harmful impurities come from heating the coal is the reason why there is so much pollution that comes from the creation of coke.
What is Coke Oven In Steel Plant?
The main function of Coke Ovens is to convert coal into coke which is used as a fuel and reducing agent in the Blast Furnace. Its secondary function is to recover Volatile Matter and CO (Coke Oven) gas from coal and extract chemicals known as Coal Chemicals. CO gas produced is used for heating purposes in the plant.
Production Field
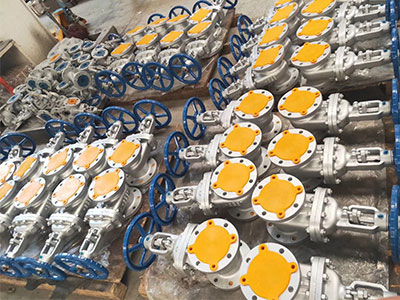
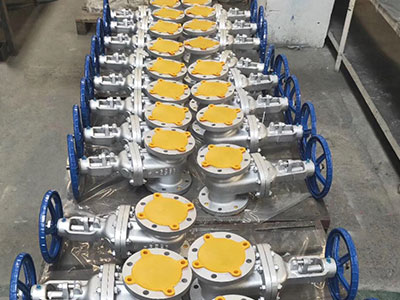
Packing List:
- Cast Steel Gate Valve 4inch~24inch
- Lug Butterfly Valve 10inch~28inch
- Motorized Ball Valve 4inch~16inch
- Flange Globe Valve 4inch~20inch
- Wafer Type NRV 10inch~28inch
Client Feedback:
ZECO Valve has provided a lot of help for our company to build the coke oven project of the JSW steel plant for pipeline valves and pipeline flow schemes.